传统工程设计效率低下,智能时代是否有破局之道?
在机械制造领域,一个长期争议的问题是:面对复杂的工程设计和日益精细的工艺要求,传统依赖人工经验的设计模式是否已到瓶颈?据行业统计,超过60%的制造企业因设计误差导致成本超支,而近半数项目因效率不足延误交付。这一背景下,超凡智控机械软件革新工程设计高效精准新视界逐渐走入行业视野。它能否真正解决设计与制造的“最后一公里”难题?我们通过三个关键问题展开探讨。
1. 效率提升:从“手工绘图”到“一键生成”?
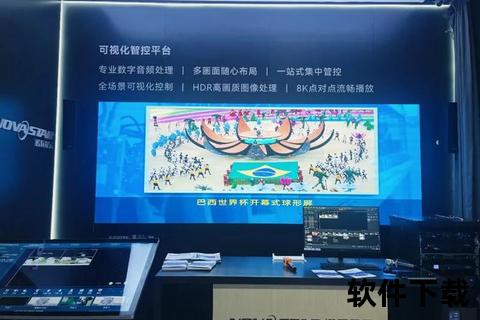
传统机械设计依赖工程师手动绘制图纸,耗时费力且易出错。以山东某机械企业为例,其皮带机集控系统设计曾因人工计算误差导致多次返工,单项目周期长达3个月。而引入超凡智控机械软件革新工程设计高效精准新视界后,通过参数化建模与AI算法优化,设计效率提升70%。例如,软件内置的“工况模拟库”可自动匹配煤矿井下环境参数,一键生成液压支架电液控制系统方案,将设计周期压缩至1个月以内。
更值得一提的是,天玛智控在煤矿无人化开采中应用同类软件,通过远程控制平台实时调整设备参数,使综采工作面调试时间从5天缩短至2小时,产能提升30%。这些案例证明,智能化工具正逐步打破效率天花板。
2. 精准控制:误差能否降到“毫米级”?
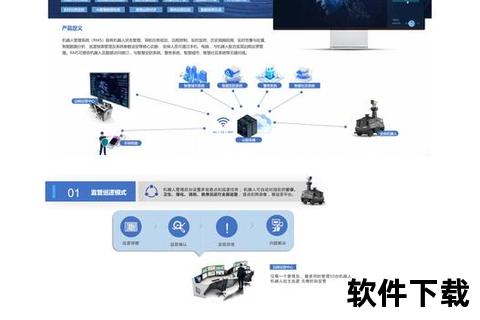
精度是机械设计的核心挑战。传统模式下,数控设备调试依赖人工经验,误差范围常达±1.5毫米。而超凡智控机械软件革新工程设计高效精准新视界通过两大创新实现突破:
动态补偿算法:三花智控在新能源汽车热管理阀件生产中,利用软件实时监测材料形变并调整加工参数,将零件精度提升至±0.02毫米,良品率从82%跃升至98%。
多场景适配:在家庭智控领域,该软件通过PLC编程实现防盗门铃与报警系统的联动控制,传感器响应误差小于0.1秒,解决了传统方案中误触率高的问题。
数据显示,采用智能控制技术的企业,产品迭代速度平均加快40%,质量投诉率下降55%。精准化不仅关乎技术,更成为市场竞争的关键。
3. 行业变革:从“单点突破”到“生态协同”?
机械软件的革新并非孤立事件,而是推动全产业链升级的引擎。例如:
跨领域融合:HW全屋智能PLC主机通过统一协议整合照明、空调、安防等子系统,用户可自定义场景联动规则,如“回家模式”中设备协同误差小于0.5秒。
数据驱动决策:天玛智控的远程运维平台累计分析超10万组矿山数据,优化出23种智能开采模型,帮助客户降低运维成本25%。
更深远的影响在于生态构建。三花智控通过软件打通制冷、汽车、储能三大业务线,实现技术复用率达65%,2023年前三季度营收增速达21.7%。这标志着行业正从单一产品竞争转向系统性能力比拼。
给企业的三条实操建议
1. 选择成熟解决方案:优先采用经过行业验证的软件平台(如天玛智控远程控制模块),避免重复投入研发成本。
2. 注重数据积累:建立设备运行数据库,通过机器学习优化参数,参考三花智控的“同源技术复用”模式。
3. 培养复合型团队:既懂机械原理又熟悉智能控制的技术人员,是落地超凡智控机械软件革新工程设计高效精准新视界的关键。
机械制造的智能化浪潮已不可逆,唯有主动拥抱工具革新,才能在高效与精准的新视界中抢占先机。