传统编程已死?智能数控车床正在改写制造规则
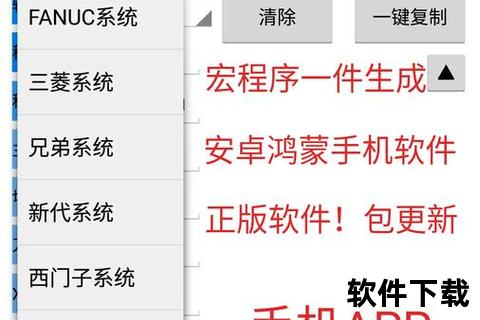
在广东某汽车零部件工厂里,操作工李师傅对着新安装的数控系统挠头——传统的手动编程需要8小时完成的曲轴加工任务,新系统竟然在15分钟内自动生成了更优化的刀路。这个场景正在全国30万家制造企业上演,引发行业激烈争论:面对精密化、个性化的生产需求,传统数控编程是否已经成为制约制造业升级的枷锁?
一、软件如何实现纳米级精准控制?
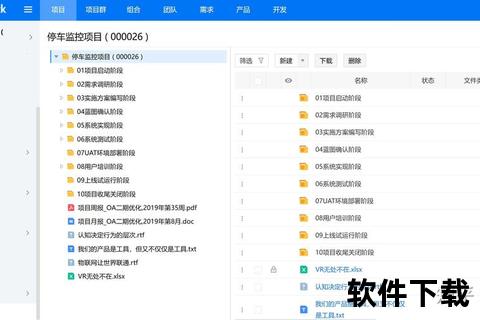
在深圳比亚迪的电机壳体生产线上,直径0.2毫米的铣刀正在雕刻比发丝还细的散热纹路。这背后是UG NX软件的实体模型全关联技术,它能将设计误差控制在±2微米以内,相当于人类头发直径的1/40。该软件特有的加工工艺参数样板库,使初、精加工参数自动匹配材料特性,成功将某型号电机壳体的报废率从3.7%降至0.5%。
更令人惊叹的是惠州某企业最新研发的CNC加工中心,通过CAMWorks的自动特征识别技术,对复杂曲面零件的编程时间缩短了68%,精度却提升到惊人的0.8微米级。这种"高效能智能优化驱动数控车床软件编程精准掌控新纪元"的技术突破,正在改写精密制造的行业标准。
二、智能优化如何突破效率瓶颈?
山东某农机企业的数字化转型案例颇具代表性。在引入WorkNC的机床仿真系统后,其轴承座加工周期从22分钟骤降至9分钟,每年节省刀具成本80万元。更关键的是,该软件的自动碰撞检测功能,使设备故障率下降了73%,这正是人工智能算法对20万次加工数据进行深度学习后的成果。
江苏某航空航天部件制造商的故事更具颠覆性。他们采用基于实例推理的智能系统后,新型钛合金零件的试制周期从3个月压缩到17天。系统通过比对历史数据库中1260个相似案例,自动优化出振动更小的切削方案,使表面粗糙度Ra值稳定在0.2μm以下。这种"高效能智能优化驱动数控车床软件编程精准掌控新纪元"的实践,让企业拿到了波音公司的长期订单。
三、技术融合会引发什么质变?
在武汉智能工厂的中央控制室,大屏上跳动着256台数控设备的实时数据。这个由5G网络支撑的工业互联网平台,将UG的加工模块与云端AI分析系统打通,实现了工艺参数的动态调整。当系统检测到某批次铝材硬度异常时,0.3秒内就完成了全车间设备的速度补偿指令下发。
更前沿的变革发生在杭州某模具企业。他们搭建的数字孪生系统,能对Mastercam生成的加工程序进行虚拟验证,提前发现92%的潜在问题。这种虚实融合的技术,使大型注塑模具的首次试模成功率从58%跃升至89%,每年减少试制材料浪费超300吨。这些案例昭示着,"高效能智能优化驱动数控车床软件编程精准掌控新纪元"正在催生全新的制造范式。
给制造业者的三条行动指南:
1. 选择软件时优先考察智能补偿功能,如Mastercam的刀尖圆弧双模补偿系统,可降低30%的刀具损耗。
2. 建立企业专属的加工参数数据库,参考CAMWorks的工艺模板架构,逐步积累智能优化所需的"数据燃料"。
3. 关注工业互联网平台与数控系统的融合应用,提前布局5G+边缘计算的协同控制体系,这是获取未来竞争力的关键。
当某新能源汽车企业用智能编程系统实现1000种电池箱体的柔性化生产时,我们清晰地看到:这场由软件驱动的制造革命,不是替代人工的冰冷机器,而是开启精密制造新维度的钥匙。那些率先拥抱"高效能智能优化驱动数控车床软件编程精准掌控新纪元"的企业,正在用代码重构产业竞争的护城河。