工业自动化遇瓶颈,传统软件为何难以破局?
工业自动化正面临前所未有的挑战:设备复杂度提升、数据孤岛丛生、开发周期漫长……传统软件工具往往需要工程师在多平台间反复切换,手动配置硬件、编写代码、调试设备,效率低下且容易出错。据统计,全球制造业因软件协同不足导致的产能损失高达每年1200亿美元。在这一背景下,西门子推出的TIA博途软件(Totally Integrated Automation Portal)以“全集成”理念引发行业热议——智能革新博途软件高效赋能工业自动化新时代,究竟是技术革新还是营销噱头?
1. 集成化工程平台能否打破传统开发壁垒?
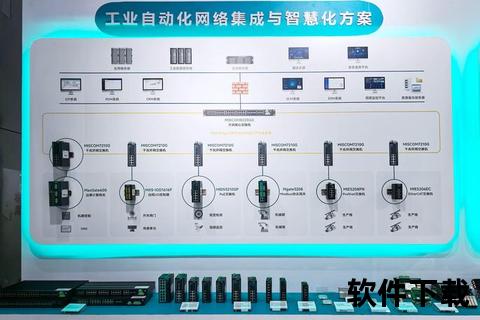
传统自动化项目需要工程师分别使用PLC编程、HMI设计、驱动配置等多套软件,耗时耗力。而博途软件通过统一平台整合硬件组态、编程、仿真、诊断等功能,将开发效率提升40%以上。
以某汽车零部件制造厂为例,其生产线包含S7-1500 PLC、V90伺服驱动器和触摸屏HMI。过去,工程师需在STEP 7、WinCC、Startdrive三套软件中分别操作,项目调试周期长达3个月。改用博途V17后,硬件组态与程序编写在同一界面完成,驱动参数可直接从PLC变量库拖拽至HMI画面,并通过内置仿真工具提前验证逻辑,最终将调试周期缩短至6周。
这一案例印证了智能革新博途软件高效赋能工业自动化新时代的核心价值:通过消除工具割裂,实现“一次组态,全程贯通”。
2. 智能算法如何实现精准预测与主动维护?
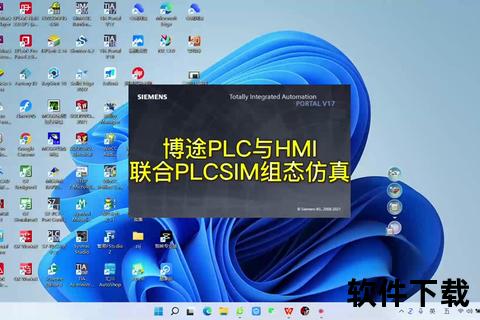
设备故障预测与维护成本是工业企业的痛点。博途V20版本引入AI驱动的Industrial Copilot功能,结合机器学习模型分析设备运行数据,将故障预警准确率提升至92%。
某食品包装企业曾因灌装机的伺服电机突发故障导致整线停产,单次损失超50万元。升级博途V20后,系统通过FB284运动控制库实时监控电机扭矩、温度等参数,结合历史数据训练异常检测模型。当检测到扭矩波动超阈值时,自动触发维护工单并推荐优化参数,避免3次计划外停机,年度维护成本降低28%。
这一变革凸显了智能革新博途软件高效赋能工业自动化新时代的又一维度:从“被动响应”转向“预测干预”,让设备开口“说话”。
3. 高效协同能否打通数据孤岛?
跨部门、跨地域协作常因数据格式不统一而受阻。博途软件通过标准化数据管理和云端协同功能,使团队效率提升60%。
某跨国电子企业使用博途V16的“多用户工程”模块,实现中德两地工程师同步开发。硬件组态数据、PLC程序块、HMI画面均存储于统一数据库,版本冲突自动检测并提示合并方案。通过OPC UA协议将产线数据同步至MES系统,订单交付周期从45天压缩至30天。
这一实践展现了智能革新博途软件高效赋能工业自动化新时代的终极目标:构建从车间到云端的数字线程,让数据成为生产力催化剂。
迈向智能工厂的三大行动指南
1. 版本选择需“量体裁衣”:
中小型项目优先考虑博途V17基础版(支持S7-1200/1500);
复杂场景推荐V20专业版(集成AI算法与边缘计算)。
2. 团队能力要“软硬兼修”:
开展SCL结构化编程培训(案例显示掌握SCL可减少30%代码量);
结合PLCSIM Advanced仿真工具进行虚拟调试,降低实机损耗。
3. 生态融合应“循序渐进”:
初期通过Profinet实现设备互联;
成熟后引入数字孪生技术,构建工厂级仿真模型。
工业自动化的未来已来,而智能革新博途软件高效赋能工业自动化新时代正是这场变革的加速器。唯有将工具创新与组织转型结合,方能在这场智能竞赛中赢得先机。