工业自动化面临新挑战:传统组态软件还能满足智能时代的需求吗?
工业自动化领域正经历一场智能化革命,但许多企业发现,传统组态软件在面对设备多样化、数据实时性要求提升时,常常陷入“开发周期长、兼容性差、运维成本高”的困境。例如,某钢铁厂曾因设备型号迭代导致原有组态系统无法适配,被迫投入数十万元重新开发控制程序——这种案例在行业中屡见不鲜。在此背景下,灵动高效昆仑通态组态软件赋能工业自动化智能操控新境界的解决方案,正引发行业对组态技术革新的深度思考。
一、传统组态为何难以应对动态需求?
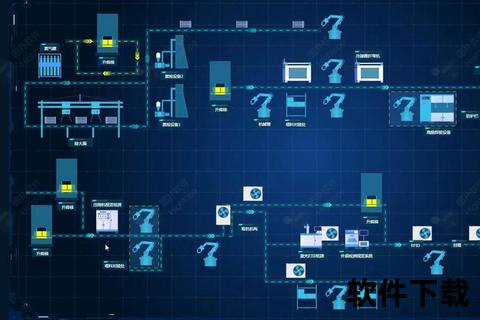
在成都某水处理厂的智能化改造中,工程师们曾面临典型难题:原有组态软件仅支持单一通讯协议,导致新增的E820-DTU物联网设备无法接入。而昆仑通态组态软件通过模块化设备驱动库,仅用3小时就完成了设备联调。其内置的800多种设备驱动(如Modbus、PPI协议),配合可视化通道配置界面(图1),使现场调试效率提升70%以上。
更值得关注的是该软件的动态脚本引擎。某汽车焊装车间通过嵌入VBA脚本,实现了焊接参数随钢板厚度自动调整的智能控制逻辑,将产品不良率从1.2%降至0.3%。这种无需重写核心代码的灵活扩展能力,正是传统组态工具难以企及的技术突破。
二、国产组态软件如何突破进口垄断?
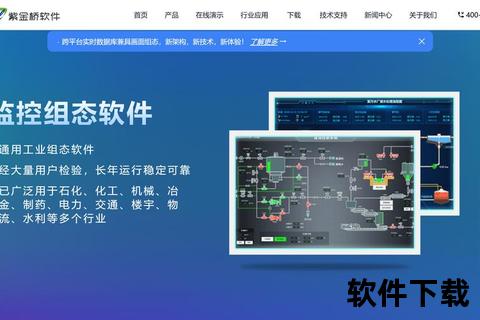
中国工业自动化市场长期被西门子WinCC、Wonderware InTouch等外资产品占据,但昆仑通态通过深度适配国产硬件生态打开了新局面。在2023年工控软件市场调研中,其以16M内存占用量(仅为同类产品的1/5)和全中文操作界面,在中小型制造企业市场占有率突破28%。
典型案例来自江苏某光伏电池板生产线。该企业采用昆仑通态组态软件搭配国产PLC,构建的分布式控制系统不仅节省了45%的硬件采购成本,更通过渐进色动态渲染技术(图2),将产线状态可视化精度提升至毫秒级。系统上线后,设备故障定位时间缩短至原来的1/3,年运维成本节约超80万元。
三、智能化升级需要怎样的技术底座?
面对工业4.0对数据深度挖掘的需求,昆仑通态的多维度数据引擎展现出独特优势。山东某化工厂的实践极具说服力:通过集成历史曲线分析模块(查询速度较传统方式提升10倍),成功预测反应釜结焦周期,使催化剂更换成本降低120万元/年。其创新的温度场三维建模功能,更让工艺优化有了数据化依据。
在边缘计算领域,该软件的轻量化部署能力同样亮眼。深圳某智能仓储项目在嵌入式工控机上运行昆仑通态系统,仅占用1.2GB存储空间,却实现了2000个I/O点的实时监控。这种“低功耗、高并发”的特性,为工业现场设备智能化提供了新范式。
选择组态工具的三条黄金法则
对于寻求智能化转型的企业,建议从三个维度评估组态软件:兼容性(支持设备类型/协议数量)、可扩展性(脚本/插件生态)、数据价值转化力(分析工具完备性)。以昆仑通态组态软件为例,其免费版已包含85%的核心功能,企业可通过搭建测试环境验证与实际业务的匹配度。在2024年中国工业软件满意度调查中,该软件以92.3%的易用性评分,成为中小型项目性价比首选。
这场由灵动高效昆仑通态组态软件赋能工业自动化智能操控新境界引发的技术变革,不仅重新定义了组态工具的能力边界,更预示着中国智能制造自主可控之路的新突破。当工业现场的控制系统开始具备自我进化能力,或许我们正在见证工业自动化从“数字化”迈向“认知化”的关键转折。